Composite Decking – “Wood” You Know the Difference?
Marilyn DeMartini, Guest Writer…
Teak is the marine industry “gold standard” for flooring and cabinetry. However, technology and material improvements in composite materials are causing builders and informed customers to look at these teak-alternatives. The numerous “faux teak” materials on the market include EVA, PVC, and polyurethane. Considered an authority, Teakdecking Systems can eliminate confusion by explaining these material differences and offering their preferred product.
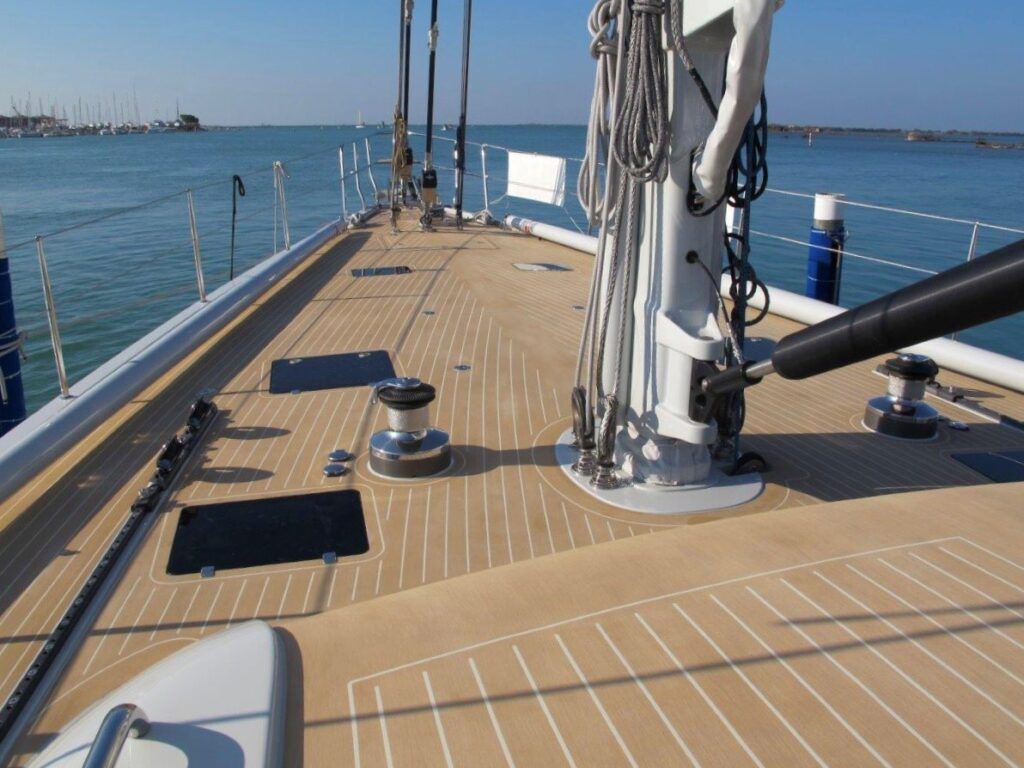
Composite Decking with Teak Look
The Teak Standard
Teak is stable, anti-slip, does not warp or rot, nor attracts insects or moisture. It is an insulator, so even heat from the sun dissipates underfoot. Teak is also sustainable when properly sourced. For example, TDS procures legally-source wood from Southeast Asia, where sustainability efforts are underway. Natural wood has a distinct advantage over petroleum-based, non-recyclable products. The latter can be less durable and very hot—especially in darker colors.
“We have been testing a variety of composites for decades,” says Alan Brosilow, VP, Teakdecking Systems. “We build for custom-designed yachts, quality production boats, and commercial vessels, and even cruise ships. Flooring must be able to expand and contract with the boat. Great applications for composite materials include large spaces, commercial vessels, or retrofits.”
– Alan Brosilow, VP, Teakdecking Systems -
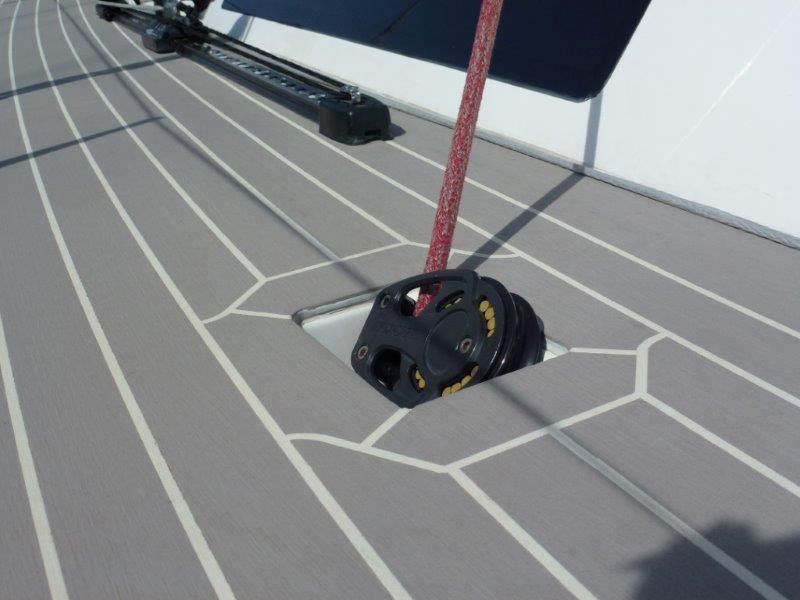
“Contemporary” battens with Composite Decking
COMPARING COMPOSITE DECKING MATERIALS
EVA (ETHYLENE-VINYL ACETATE/POLYETHYLENE)
EVA an elastic, closed-cell foam, is known for its rubbery softness. The sheets are cut to fit and its adhesive backing holds it to the floor. EVA’s stability and durability, however, can be compromised by extreme marine elements of sun and moisture—especially in larger-sized boats. While EVA flooring is cushioned and comfortable to bare feet, it often pulls up on the corners and is less durable than harder surfaced decks.
PVC (POLYVINYL CHLORIDE)
PVC comes in strip planks, heat welded together, that are cut, fit, and finished for labor-intensive installation. PVC doesn’t warp or splinter like real wood and it is durable. But in the marine environment, it has been known to lose color and since it is welded together, welds have been known to separate. Though it is UV resistant to a point, it has a thin profile and can show any deck imperfections, and it does not stand up to regular maintenance or sanding. Since PVC is usually installed with butt joints, it lacks the integrity of the more detailed and time-consuming finger joints (in which TDS takes pride).
While using a product like EVA or PVC may save up to 25% of the cost, TDS maintains that the customers receive greater value and longevity, using higher-quality polyurethane (especially on large boats).
-Alan Brosilow, VP, Teakdecking Systems-
POLYURETHANE
Polyurethane decking is preferred by TDS because it is durable and can be assembled in long lengths, using finger joints, and the exact-fit template is installed like the company’s signature teak, in pre-fit, digitized panels. TDS uses polyurethane brands like Esthec or Herculan because they can be cut into any customized shape on a CNC machine and placed on a deck that receives high traffic, like a helipad, tender garage, or yacht beach clubs. These materials are highly durable, water- and UV-resistant, and repairable.
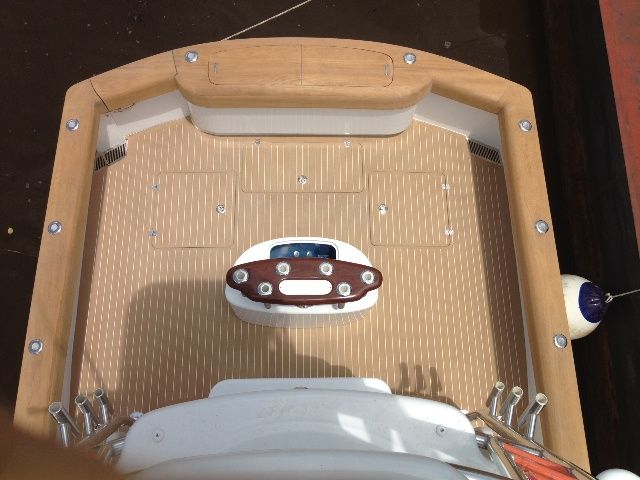
Composite decking requires less maintenance
PROPERTIES
Stains – All composites, like teak, can be stained by oils or red wine.
Sanding – Polyurethane flooring is thick. It can be sanded to open the pores, washed with mild soap and water, and even lightly pressure washed to maintain its finish. Polyurethane is repairable, and the colors “weather” making repairs nearly unnoticeable. Lighter colors like “biscuit” are preferable to darker “honey” colors that may look like oiled teak because they are cooler underfoot.
“Some manufacturers were using cheaper materials, but for the more knowledgeable customer, they changed to the more expensive product, rather than replace it in 2-3 years,” says Brosilow. “Saltwater exposure makes the edges break away as they get ‘crispy’ and the flooring peels, contrasting with polyurethane which can last up to 20 years.”
IT’S NOT JUST THE WHAT–IT’S THE HOW.
With 40 years of experience, TDS has learned how to properly install decks. This is as important as the decking material itself. For example, TDS addresses the typical gelcoat line from the boat mold. Most installers just lay decking over the depression from the mold, using acetone to remove the wax but not modifying the surface. TDS sands the gelcoat surface to ensure a solid bond. TDS has applied commercial-grade polyurethane to large custom flooring applications, and also manufactured custom parts like cap rails, covering boards, and steps.
Teakdecking System’s long-standing reputation was earned with the modular construction of decking, innovative proprietary adhesives, and award-winning caulking. These decking materials coupled with installation expertise achieve lasting results for its customers, in teak or composite. No matter the material, customers can depend on the expertise and reliability of Teakdecking Systems.
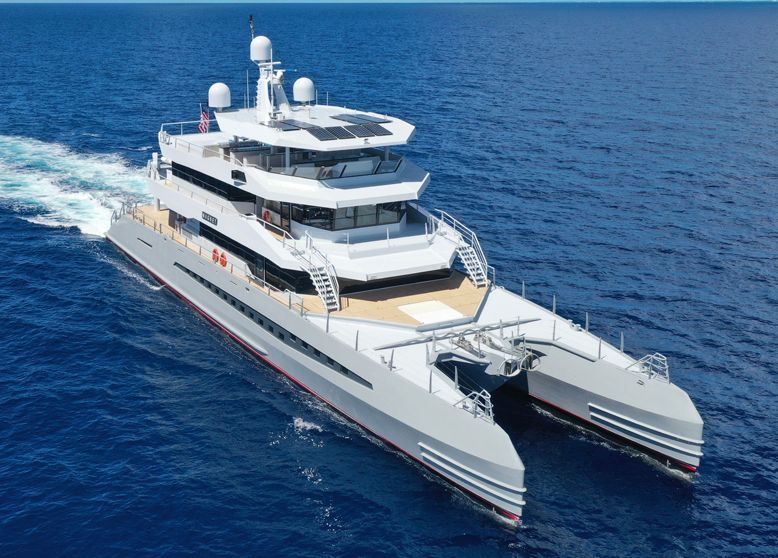
Metal Shark Yacht with Composite Decking (polyurethane)
ADDITIONAL THOUGHTS FROM TDS
EVA and PVC are good, cost-effective choices for small vessels. But for the optimal UV and water-resistance, polyurethane is the better choice, especially on large boats because it is chemically resistant, durable, and repairable.
To read more, please go to this article: How to Compare Teak and Composite Decking
QUESTIONS? PLEASE CONTACT US
yacht.services@teakdecking.com
941-756-0600
ALL PRODUCTS
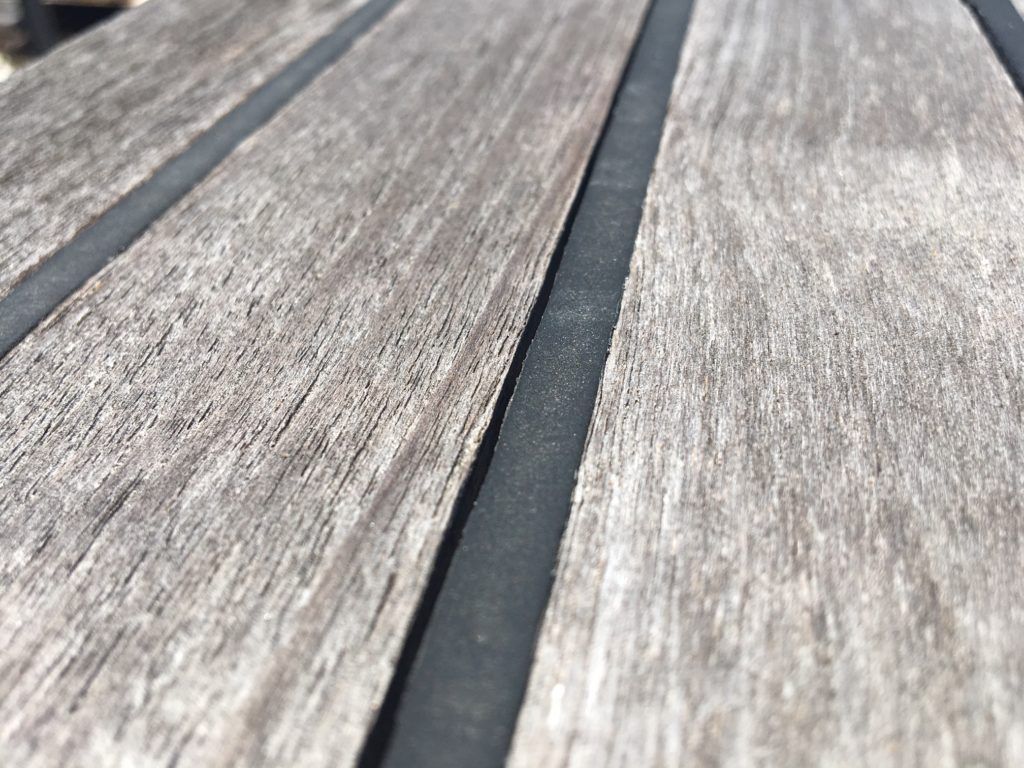