How to Recaulk Seams
“I’d rather burn my boat to the waterline before I recaulk seams again,” a boat owner said to our Sales Manager at a recent boat show.
Then the boat owner laughed and said, “Of course, my family and I love the Hylas 54 too much to do this. But I sure did have some frustrations, largely my fault. It was my first recaulking job, and it was a big one with nearly one mile of seams.”
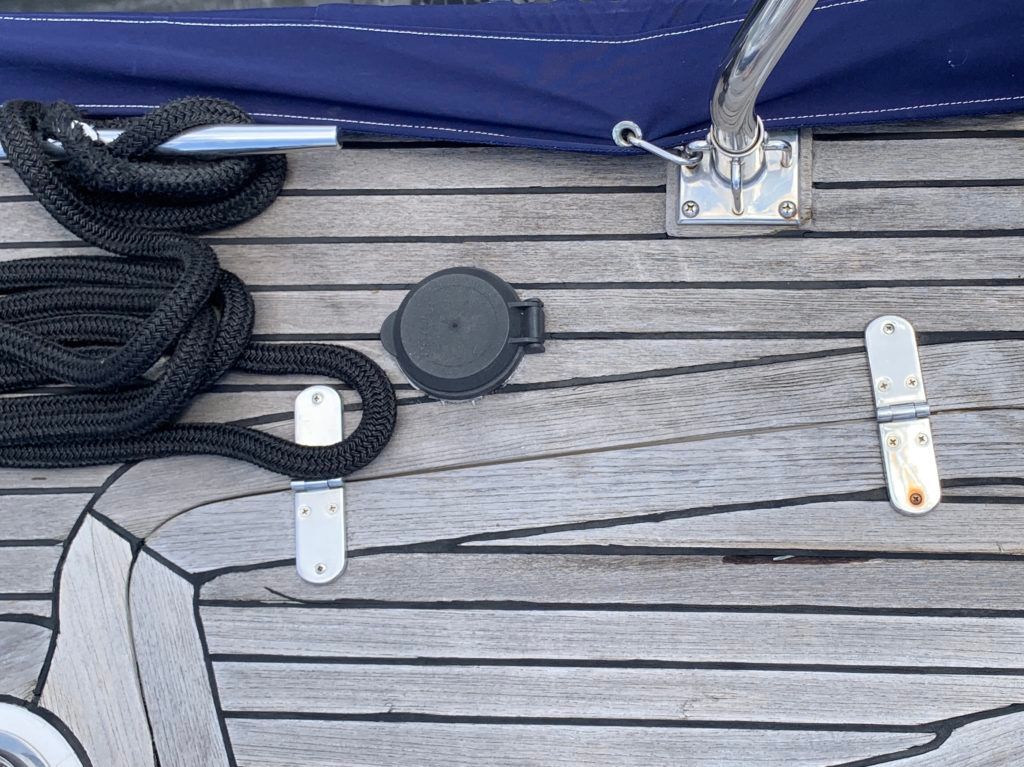
Aged teak deck
At TDS, we understand that it’s a big job. An aging teak deck can have proud caulking. Scuffing a foot on the deck could loosen the caulk. Or tugging on the caulking will easily pull it up. Additionally, if caulk has separated from the teak planking, it will eventually loosen if not repaired. These gaps will trap water and potentially cause damage.
We have perfected the art of caulking and want to share advice to prevent frustrations like those of the owner at the boat show. Here, we provide some time-tested tips, and if you call us, we will walk you through the process. We want your re-seaming project to be a success.
SIS 440 Caulking, a proprietary formulation, expands and contracts with boat movement and temperature changes. Caulk is designed to do this.
Teak naturally wears 0.25 to 0.5 mm/year, which will cause the caulking to become “proud.” So, it is essential to watch the deck as it ages and to perform a light sanding for periodic maintenance. This sanding will remove the proud caulk and keep the teak surface smooth. A smooth teak surface prevents trapping dirt.
BEFORE STARTING TO RECAULK SEAMS TAKE THESE NECESSARY STEPS
1) DETERMINE THE DEPTH OF THE SEAM
Seams should have a depth of 5/16 to 1/2” (8-12 mm)* for recaulking to be successful (and cost-effective). Do not fill shallow seams because there could be adhesion problems.
*Seams sizes could vary with larger and thicker planks.
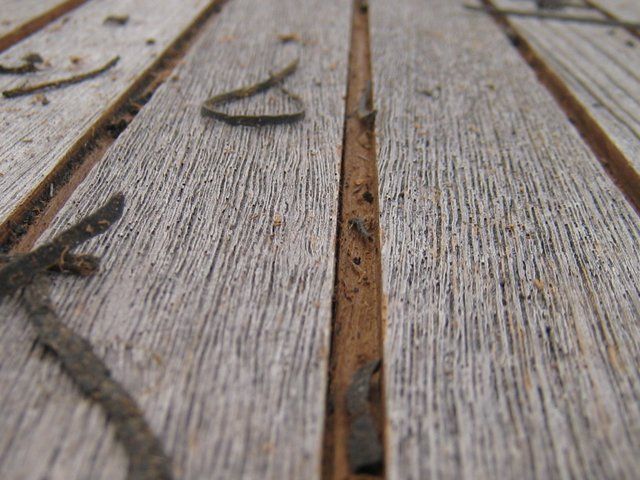
Seam is too shallow for re-caulking
2) CHOOSE THE BEST LOCATION FOR TO RECAULK SEAMS
Always work under a cover. Ideally indoors for protection from rain or snow. Indoor temperature control will enhance caulk cure time. Ideally, the temperature should be 40-90°F or 5-33°C. If unable to work under a cover, only open as much seam as can be cleaned and recaulked on the same day.
3) SAND THE DECK
Before beginning to recaulk seams, a light sanding of the deck creates a smooth surface so that caulking does not fill any ridges in the teak. This pre-sanding will make the final sanding (after re-caulking) much easier, saving time.
4) REMOVE HARDWARE
Since sanding is required before and after recaulking, the hardware will rest on proud teak if it is not removed.
5) READ THE APPLICATION INSTRUCTIONS ON THE CAULK PACKAGING
Instructions are carefully written to help users (with SIS 440).
REMOVING OLD CAULKING
Remove ALL caulk to prepare clean seams of fresh wood for new caulk. For small jobs, remove caulk with a razor and reefing hook.
For large jobs, electric tools are better. A Fein tool with a teak caulk removal blade works well. For experienced users, a saw or router can be used.
Regardless of the tool, work carefully to not gouge the edges of the seams. Then, the seams MUST be sanded, vacuumed, and cleaned with acetone. Fresh, clean wood ensures optimal adhesion.
BOND BREAKER TAPE IN SEAMS
Place bond breaker tape at the bottom of the seam. The tape prevents an adhesive bond of the caulking to the bottom of the seam, allowing movement during caulk expansion and contraction.
FILLING THE SEAMS
The temperature must be at least 40°F (5°C) when caulking. Fill seams with a manual gun, electric gun, or pneumatic gun. Regardless of the gun type, cartridge tip preparation is the same.
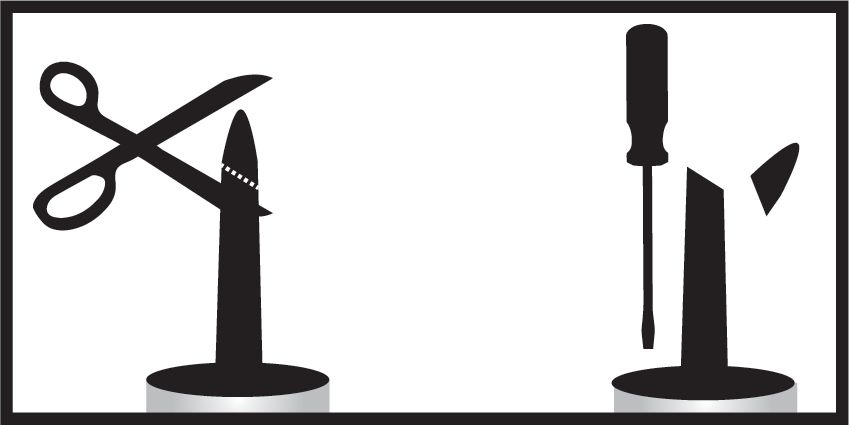
Cut the tip of the cartridge at an angle. Then insert a screwdriver to puncture the foil lining. After completing this, squeeze the tip to flatten it. This will help to align the tip with the seam. NOTE: Fully open the tip and foil, or caulk may push out from the back of the cartridge.
Begin application and ensure caulking goes to the bottom of the seam, allowing it to flow upward until crowning above the top of the seam. Smoothly pull the gun along the seam toward the applicator. Avoid starts and stops or changes in direction that may entrap air.
If using a pneumatic caulk gun, do not exceed 80 psi to prevent overriding the plunger and injection air into the caulk.
Immediately after applying the caulking, draw a flexible putty knife over the seam. Apply enough pressure to make sure caulk fills to the bottom of the seam, and then crowns to allow for slight settling. Make sure the seams have no entrapped air after application. Do not disturb the caulking until fully cured.
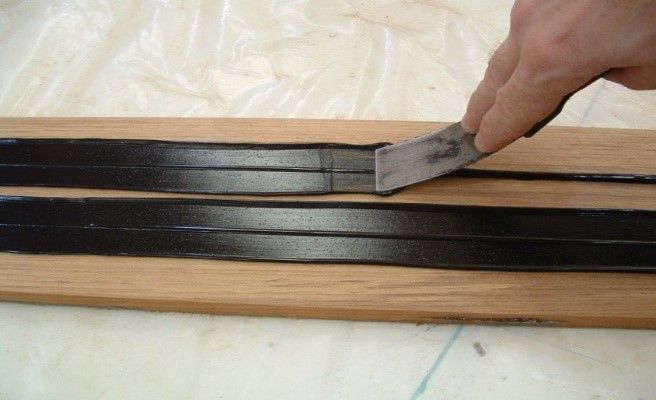
Apply pressure to fill seam. Be sure that caulking crowns.
Masking the teak before caulking may be done. Place tape 1 mm from the edge of the seam. Note: It will require more pressure to fill the seam with the putty knife with a masked edge.
CURING
Cure time is a function of the cross-sectional dimension of the seam and ambient temperature and humidity. Cold or very dry air will increase the cure time. Caulking cures from the top down at a rate of about 1-2 mm/day with a maximum rate of 3mm/day. Allow at least 48 hours. White and gray will take longer, so please read about these special considerations at https://teakdecking.com/caulk/
SANDING AND FINISHING
Sand using 80-100 grit sandpaper with a soft pad on a grinder. Do not use orbital and belts sanders because they may “dig” into the teak. A Fein tool with a sanding pad is good for the corners. Hand-sanding is required for details that cannot be reached with power tools. Rich brown teak and razor-sharp seams appear as the caulking is sanded away.
If there are gaps, bubbles, or under-filled seams, it is due to improper caulking. The seams were not filled properly or did not cure adequately.
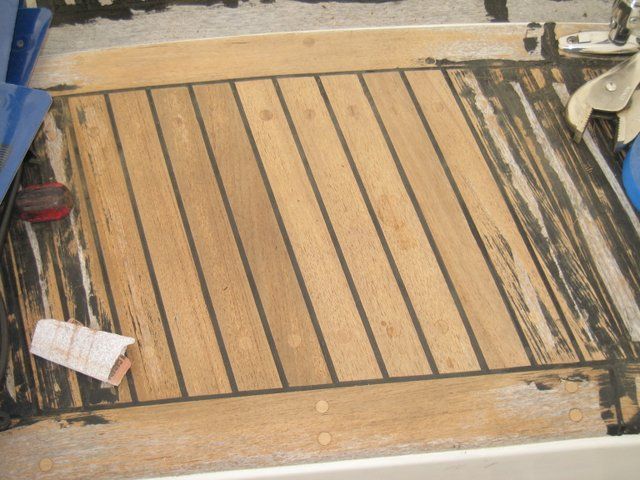
This deck was not sanded before recaulking, making it difficult to sand off the caulking
We want your project to be successful. To recaulk seams, follow these recommended guidelines and read our free 16-page Caulking Guidebook: Teakdecking.com/caulk. Or Call us if you have questions and we will walk you through the process.
Read more articles:
How to Inspect Teak Deck Caulking and Seams
Application Techniques for Gray and White Caulking
What is the Caulk Yield for Teak Deck Caulking
CONTACT TEAKDECKING SYSTEMS
941-756-0600
products@teakdecking.com
The Professional’s Choice
ALL PRODUCTS
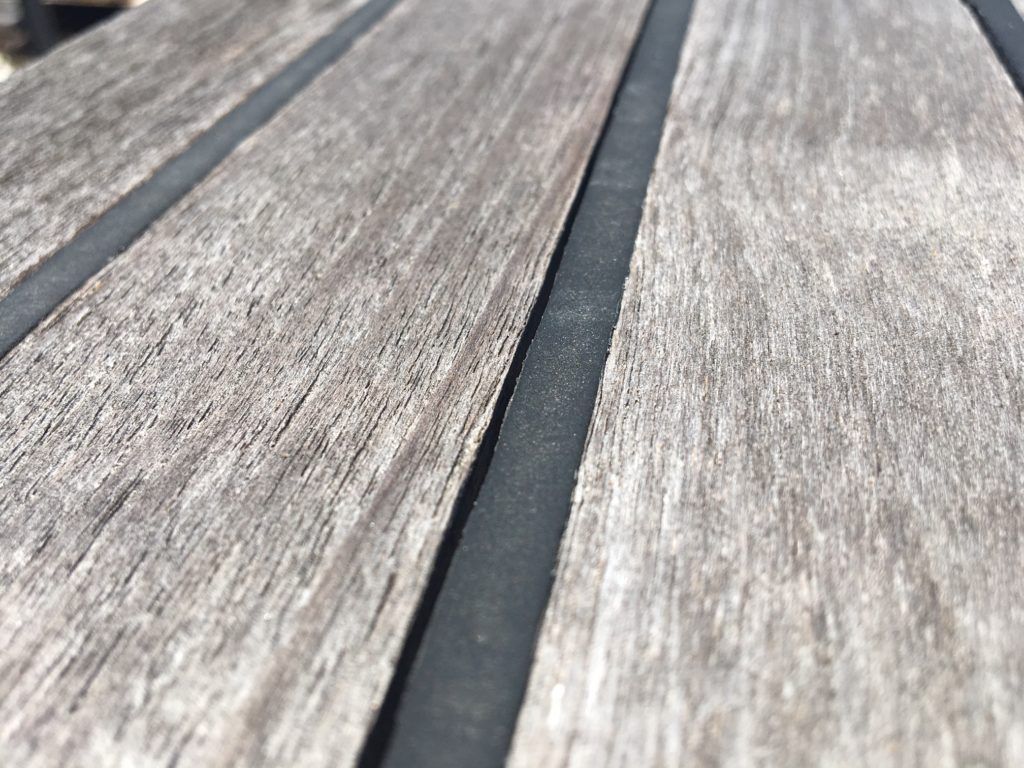